고성능 반도체 소재인 탄화규소(SiC)는 우수한 물리적, 화학적 특성으로 인해 전력 전자, 무선 주파수 마이크로파, 광전자공학 및 기타 분야에서 큰 응용 가능성을 보여줍니다. 그러나 탄화규소의 높은 경도와 안정적인 격자 구조는 연마 공정에 큰 어려움을 안겨줍니다. 본 논문에서는 탄화규소 기판 연마가 어려운 이유에 초점을 맞춰 관련 분야의 연구 및 응용에 참고 자료를 제공하고자 한다.
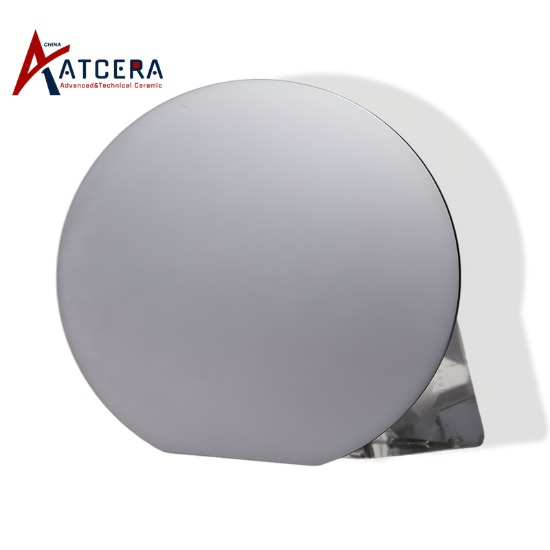
첫째, 연마문제로 인한 높은 경도와 취성
탄화규소의 초고경도는 놀라운 특성 중 하나이며, 모스 경도는 최대 9.5로 다이아몬드에 이어 두 번째입니다. 이러한 높은 경도 특성으로 인해 연마 공정에서는 동일한 경도의 연마재와 도구를 사용해야 합니다. 그러나 경도가 높은 연마재는 연마 과정에서 연마 도구의 급격한 마모로 이어지는 경우가 많으며, 이는 연마 효율성을 감소시킬 뿐만 아니라 연마 품질 저하로 이어질 수도 있습니다. 또한 탄화규소의 취성도 연마 공정에서 큰 문제가 됩니다. 연마 공정에서 SiC 기판은 균열이 발생하여 표면 손상 및 균열이 발생하기 쉽습니다. 이러한 결함은 웨이퍼의 외관 품질에 영향을 미칠 뿐만 아니라 전기적 성능 및 신뢰성에도 영향을 미칠 수 있습니다.
둘째, 안정된 격자구조로 인한 연마의 어려움
SiC의 격자 구조는 Si-C 사면체로 구성되어 밀집된 구조와 높은 안정성을 가지고 있습니다. 이러한 안정된 격자 구조로 인해 외부 가공 수단으로 표면 구조를 변경하는 것이 극히 어렵습니다. 연마 공정에서 Si-C 원자 사이의 공유 결합을 끊고 재료 제거 및 표면 품질 향상을 달성하려면 많은 열 에너지와 마찰 전단력을 소비해야 합니다. 이는 폴리싱 공정에 드는 에너지 소모와 시간 비용을 증가시킬 뿐만 아니라, 칩 내부 구조에 손상을 줄 수도 있다.
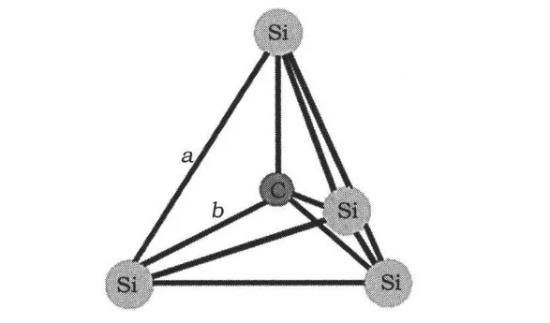
셋째, 연마과정에서 응력의 영향
전통적인 연마 공정에서는 일반적으로 공작물과 연마 다이를 접착 접착제로 고정합니다. 그러나 SiC 기판과 연마 다이 사이의 열팽창 계수가 일관되지 않기 때문에 냉각 및 경화 후 접합 부위에 응력이 발생합니다. 이러한 응력은 연마 중 웨이퍼 표면의 모양과 마감에 악영향을 미치고 결과적으로 연마 품질이 저하됩니다. 또한, 연마 공정 중 발생하는 마찰열과 기계적 응력은 이러한 효과를 더욱 악화시켜 연마 공정의 제어를 더욱 어렵게 만들 수 있습니다.
넷째, 연마액과 연마패드의 선택
연마액과 연마 패드는 연마 공정의 핵심 요소이며 이들의 선택은 연마 효과에 직접적인 영향을 미칩니다. 탄화 규소 기판의 경우 경도와 취성이 높기 때문에 기존 연마액과 연마 패드는 연마 요구 사항을 충족하기 어려운 경우가 많습니다. 한편으로는 칩의 과도한 손상을 방지하기 위해 연마액의 조성, 입자 크기 및 연마재 농도를 정밀하게 제어해야 합니다. 한편, 최고의 연마 효과를 얻으려면 연마 패드의 경도, 탄성 및 표면 지형도 탄화규소 기판의 특성과 일치해야 합니다. 그러나 SiC 기판용 특수 연마액과 연마 패드는 아직 시장에 부족하여 연마 공정의 난이도와 비용이 더욱 증가하고 있다.
요약하면 탄화 규소 기판 연마가 어려운 이유는 주로 높은 경도와 취성, 안정적인 격자 구조, 연마 공정에서의 응력 영향, 연마 유체 및 연마 패드 선택 등이 있습니다. 이러한 과제는 SiC 기판의 연마 효율성과 품질에 영향을 미칠 뿐만 아니라 관련 분야에서의 적용 및 개발도 제한합니다. 따라서 이러한 문제를 극복하고 탄화규소 소재의 폭넓은 응용과 개발을 촉진하기 위해서는 향후 탄화규소 기판 연마 기술에 대한 연구와 혁신을 강화할 필요가 있다.