빠르게 발전하는 전자 산업에서 알루미나 기판은 우수한 절연 특성, 화학적 안정성, 높은 열 전도성 및 우수한 고주파 특성을 갖춘 전자 부품에 없어서는 안될 기판이 되었습니다. 이는 전자 부품을 지지할 뿐만 아니라 방열 및 절연에도 중요한 역할을 합니다. 그러나 고품질 알루미나 세라믹 기판을 준비하는 과정은 복잡하고 정교합니다. 원료 공식, 캐스팅 필름 두께 및 소결 공정 매개 변수와 같은 핵심 요소는 제품의 두께 균일성, 외관 품질 및 표면 거칠기에 직접적인 영향을 미치며 제품의 전반적인 성능을 결정합니다. 이 글에서는 알루미나 세라믹 기판 준비 공정을 최적화하기 위한 참고 자료를 제공하기 위해 세 가지 주요 첨가제인 결합제, 가소제, 분산제의 효과와 공정 제어에 대해 논의했습니다.
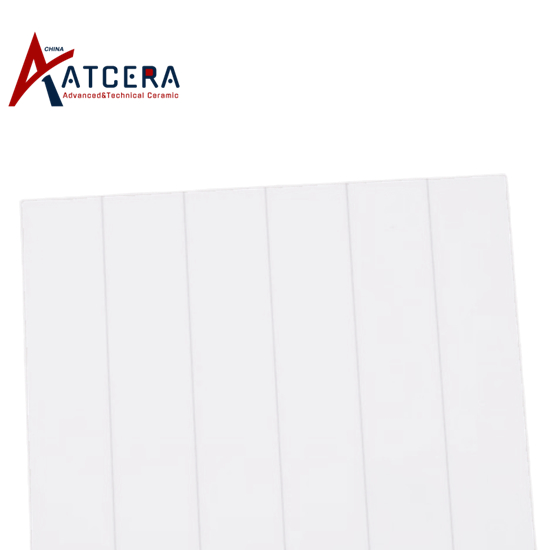
바인더 선택 및 첨가량 조절
세라믹 시트의 3차원 네트워크 구성을 위한 주요 유기 첨가제로서 바인더는 선택된 용매에 용해되어야 하며 일반적인 유형에는 폴리에틸렌, 폴리비닐 알코올 등이 포함됩니다. 캐스팅 그린의 외관, 가공 특성 및 다공성에 미치는 영향 빌렛의 바인더 첨가량은 제품의 성능에 미치는 영향을 종합적으로 고려해야 합니다. 바인더의 적절한 양은 그린 빌렛의 강도와 인성을 보장할 수 있지만 바인더가 너무 많으면 탈지가 어려워지고 그린 빌렛 밀도가 감소하여 완제품의 수축률과 기계적 특성에 영향을 미칩니다. 너무 적으면 분말을 효과적으로 접착시킬 수 없습니다.
가소제의 도입과 균형
가소제는 바인더의 소성한계온도를 낮춤으로써 캐스트 필름의 유연성과 작업성을 향상시키고, 건조 후 인성이 부족한 문제를 해결하며, 슬러리의 안정성을 향상시킵니다. 그러나 가소제의 첨가는 필름 강도의 과도한 감소를 피하기 위해 적당해야 합니다. 이상적인 가소제는 페이스트의 다른 성분과 조화를 이루는 안정적인 물리화학적 특성을 가져야 하며 성능을 유지하면서 첨가를 최소화해야 합니다.
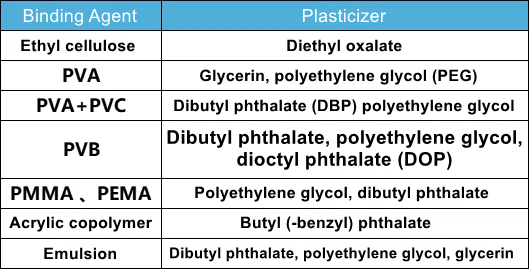
일반적인 바인더는 가소제에 해당합니다
분산제의 선정 및 투여량 조절
슬러리 내 분말의 양호한 분산은 고품질의 알루미나 세라믹 기판을 제조하는 기초입니다. 분산제는 정전기 및 입체 장애를 통해 입자의 현탁을 촉진하고 안정적으로 분산시킵니다. 슬러리 시스템에 따라 올바른 유형의 분산제(예: 무기, 유기, 고분자 및 복합 분산제)를 선택하는 것이 중요합니다. 분산제 첨가량은 알루미나 분말의 크기에 따라 조절되며, 미세입자는 표면에너지가 크기 때문에 일반적으로 더 많은 분산제가 필요하다.
요약하면, 결합제, 가소제 및 분산제의 선택 및 공정 제어는 알루미나 세라믹 기판을 준비하는 동안 최종 제품의 성능에 결정적인 영향을 미칩니다. 알루미나 세라믹 기판의 두께 균일성, 외관 품질 및 표면 거칠기는 최적화된 주조 필름 두께 및 데스점성 소결 공정 매개변수와 결합하여 이러한 첨가제의 유형과 양을 정밀하게 조절함으로써 효과적으로 개선될 수 있으며, 이를 통해 전자 분야에서 탁월한 성능을 보장할 수 있습니다. 구성 요소. 미래에는 재료 과학 및 준비 기술의 지속적인 발전으로 첨가제 공식 및 공정 매개변수의 추가 최적화로 더 넓은 범위의 분야에서 알루미나 세라믹 기판을 적용할 수 있는 새로운 가능성이 열릴 것입니다.