반도체 장치에 탄화규소(SiC)가 광범위하게 적용됨에 따라 탄화규소 기판의 품질 요구 사항이 점점 더 엄격해지고 있습니다. SiC 소자는 라이너 필름의 표면 두께 변화, 표면 거칠기(Ra), 가공 손상 및 잔류 응력에 대해 엄격한 규정을 가지고 있습니다. 그러나 절단 및 박리 후 SiC 기판은 층 손상, 높은 표면 거칠기 및 낮은 평탄도와 같은 문제를 갖는 경우가 많습니다. 이러한 문제는 후속 에피택시 공정을 위한 고품질 연마 시트를 얻기 위해 효과적인 평탄화 공정을 통해 해결되어야 합니다. 이 기사에서는 SiC 기판 평탄화 공정의 연삭 및 연삭 기술에 초점을 맞추고 그 장점과 단점을 비교 분석합니다.
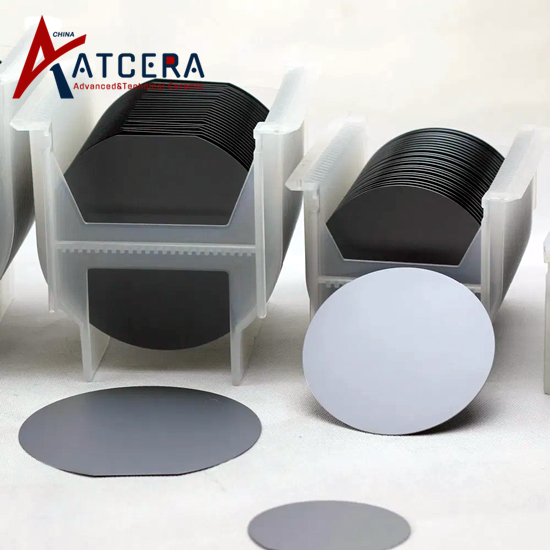
1. 분쇄공정의 현황과 한계
연삭 공정은 거친 연삭과 미세 연삭의 2단계로 시장 점유율이 높으며, 화학 기계적 연마(CMP) 이전에 단면 기계적 연마(DMP)가 필요합니다. 비용이 상대적으로 저렴하다는 장점이 있지만, 번거로운 프로세스, 낮은 자동화 수준, 높은 단편화 위험, 낮은 유연성, 환경에 대한 특정 영향 등의 단점이 있습니다.
2. 분쇄공정의 장점과 적응성
연삭 공정의 대안인 연삭 공정은 더 높은 재료 제거율과 더 나은 웨이퍼 두께 및 평탄도 제어를 제공합니다. 다이아몬드 연삭 휠과 같은 다양한 연마재 및 연삭 기술을 사용하여 더 미세하고 균일한 표면 처리를 달성합니다. 연삭 공정은 자동화 및 유연성 측면에서 우수하며 단일 칩 처리에 적합하며 대형 웨이퍼의 처리 요구에 더 잘 적응할 수 있습니다.
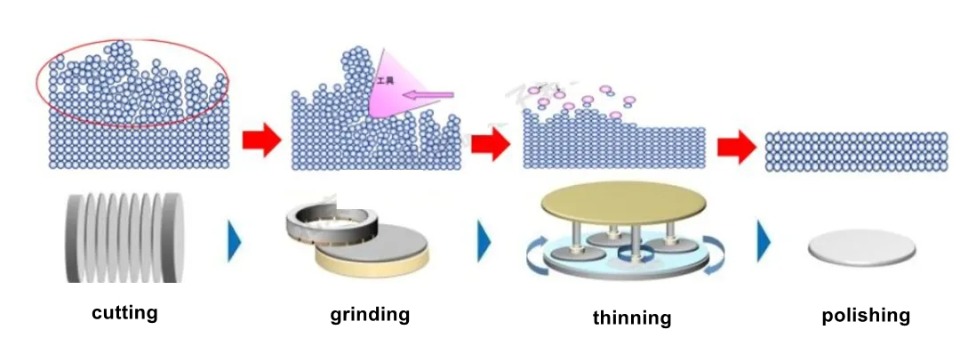
SiC 기판 평탄화 공정도
연삭 공정은 일반적으로 거친 연삭과 미세 연삭의 두 단계로 구성되며, 기판 표면의 손상된 층은 연마재의 입자 크기에 따라 점차적으로 제거되어 표면 평활도를 향상시킵니다. 그러나 그 과정에는 문제가 많다. 우선, 거친 연삭부터 미세 연삭, DMP 및 CMP까지 공정이 더 복잡하고 여러 단계가 필요하여 처리 시간과 비용이 증가합니다. 둘째, 자동화 수준이 높지 않아 생산 효율성이 낮다. 대형 웨이퍼의 경우 가공 중 기계적 스트레스로 인해 조각화될 위험이 높습니다. 또한 연삭 공정의 유연성이 낮아 단일 칩 가공에 적합하지 않으며 연삭 유체의 사용은 환경에 일정한 영향을 미칩니다.
연삭 공정에서는 다이아몬드 휠과 같은 매우 효율적인 연마재를 사용하여 더 높은 재료 제거율로 SiC 기판을 빠르게 평탄화합니다. 연삭 공정에 비해 연삭 공정은 다음과 같은 장점이 있습니다. 첫째, 자동화 수준이 높아 생산 효율성을 크게 향상시킬 수 있습니다. 두 번째는 유연성이 뛰어나 단일 가공에 적합하며 다양한 요구에 따라 맞춤화할 수 있습니다. 셋째, 대형 웨이퍼의 처리 요구 사항에 더 잘 적응하고 조각화 위험을 줄일 수 있습니다. 또한, 연삭 공정을 통해 더 미세하고 균일한 표면 마감이 가능해 후속 CMP 공정에 더 나은 기판을 제공합니다.
요약하면, SiC 기판 평탄화 공정의 연삭 및 연삭 기술에는 장점과 단점이 있습니다. 분쇄 공정 비용은 저렴하지만 공정이 번거롭고 자동화 수준이 높지 않으며 단편화 위험이 높고 유연성이 낮아 추가 개발이 제한됩니다. 이와 대조적으로 연삭 공정은 자동화, 유연성, 재료 제거율 및 표면 처리 품질 측면에서 분명한 이점을 보여주며 이는 현대 반도체 산업에서 SiC 기판의 고품질 요구 사항에 더 적합합니다. 따라서 반도체 기술의 지속적인 발전에 따라 연삭 공정은 SiC 기판 평탄화의 주류 기술이 될 것으로 예상됩니다. 앞으로는 SiC 장치의 점점 더 엄격해지는 기판 요구 사항을 충족하기 위해 처리 효율성과 품질을 향상시키기 위해 연삭 공정 매개변수를 더욱 최적화해야 합니다.