다른 산화물 세라믹 멤브레인 (알루미나, 산화티타늄, 지르코니아 등)과 비교하여 탄화규소 멤브레인 튜브는 친수성, 투과성, 내오염성 및 화학적 안정성이 더 높습니다. SIC 세라믹 멤브레인의 소결 온도는 소결 기술과 밀접한 관련이 있으며 일반적인 소결 기술에는 재결정 기술, 세라믹 전구체 전환 기술 및 현장 반응 소결 기술이 포함됩니다.
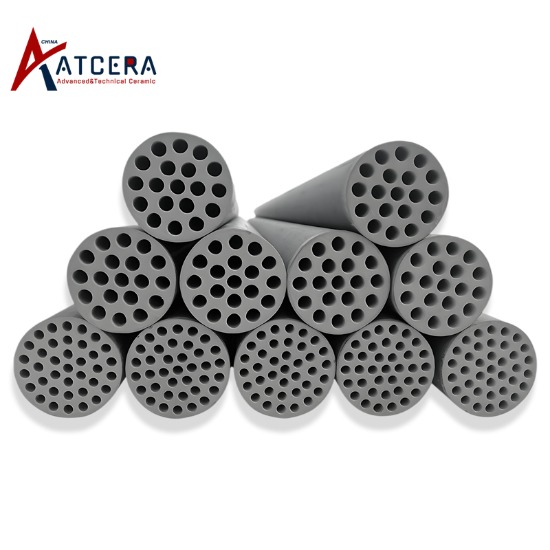
재결정 소결 기술
재결정 소결 기술은 고온 소결 하에서 증발-축합 기상 이동 메커니즘에 따라 SIC 입자의 재결합을 구현하는 것을 의미합니다. 이 공정은 너무 많은 화학 반응을 수반하지 않으며, 기공 크기는 원료 분말의 크기에 크게 영향을 받으며, 얻은 탄화 규소 막 기공 구조는 균일하고 지그재그 계수가 낮습니다. 탄화규소는 고온, 고압 및 넓은 pH 범위에서 안정성이 우수하므로 일반적으로 재결정 중 소결 온도를 낮추기 위해 소결 첨가제 및 탄화규소 분말의 이중 피크 분포가 사용됩니다. 재결정 소결 기술로 제조된 탄화규소 막 튜브는 화학적 안정성이 높지만 소결 온도가 높고(> 1800℃) 에너지 소비가 크고 소결 공정 중 불활성 분위기 보호가 필요하며 장비가 매우 까다롭습니다. 엄격한. 또한, 기공 내에 잔류할 수 있는 탄소를 제거하기 위해서는 소결 완료 후 800℃ 이하의 공기분위기에서 표면산화를 진행해야 하므로 제조과정이 복잡해진다.
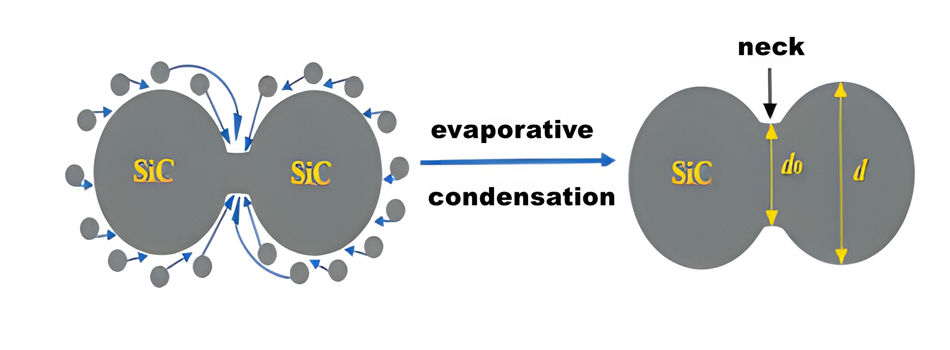
SiC 고온 재결정 다이어그램
세라믹 전구체 변환 기술
세라믹 전구체 전환 기술은 불활성 분위기와 특정 온도 범위(1100~1600℃)에서 실리콘 함유 유기 고분자(예: 실리콘 수지, 폴리카보실란 등)를 분해하여 탄화규소 집합체 사이에 결합상을 형성하는 기술을 말합니다. , 탄화 규소 세라믹 막의 ac 및 특정 기계적 강도를 준비합니다. 세라믹 전구체 변환 기술은 소결 온도 요구 사항이 낮아 에너지 소비를 줄이는 데 도움이 됩니다. 그러나 원료가 고분자이고 소결 공정에는 혐기성 분위기가 필요하므로 비용이 많이 들고 공정이 복잡하다는 단점이 있어 산업 생산에 도움이 되지 않습니다. 멤브레인 생산을 위한 세라믹 전구체 전환 기술의 적용 가능성을 더욱 개발하고 최적화하기 위해서는 비용 절감 및 미세 구조 규제(기공 크기, 다공성 및 멤브레인 두께)에 중점을 둘 필요가 있습니다.
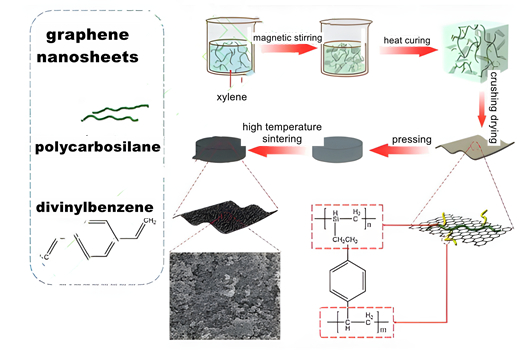
세라믹 전구체 전환 기술을 이용한 탄화규소 세라믹 분리막 제조
현장 반응 소결 기술
현장 반응 소결 기술은 공기 분위기 하에서 탄화규소 집합체 입자에 소결 첨가제를 첨가하여 순상 탄화규소 세라믹 막의 소결 온도(1350~1550℃)보다 훨씬 낮은 온도에서 산화규소를 생성하는 기술을 말하며, 그런 다음 소결제와의 현장 반응을 통해 목 연결을 형성합니다. 일반적인 소결 첨가제는 주로 알루미나, 산화 이트륨 및 지르코니아와 같은 금속 산화물입니다. 반응 과정에서 멀라이트, 근청석 및 기타 다성분 산화물은 입자 간 목 연결의 결합 단계가 됩니다. 이러한 소결 첨가제의 첨가는 SIC 골재의 결정립계 및 표면 에너지의 변화에 도움이 되어 소결 공정에서 질량 확산 속도를 가속화하고 소결 비용을 절감합니다. 현장 반응성 소결 기술은 SIC의 소결 온도를 효과적으로 낮출 수 있지만 막 준비 과정은 여전히 단축되어야 합니다.
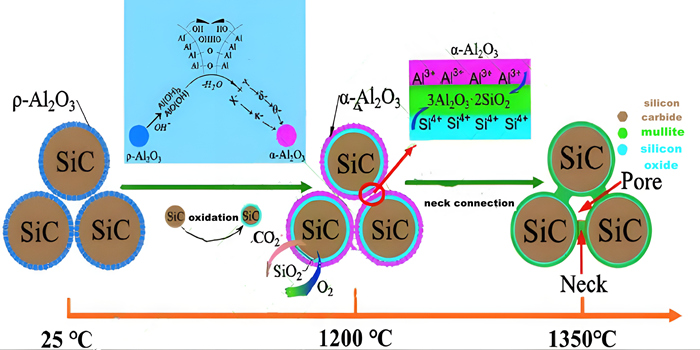
현장 반응성 소결 기술로 제조된 멀라이트 결합 다공성 탄화규소 세라믹의 소결 공정 모식도
탄화 규소 막 튜브의 산업적 적용 가능성을 더욱 향상시키기 위해서는 비용 절감 및 성능 향상 측면에서 고려할 수 있습니다. 예를 들어, 비용을 줄이기 위해 작은 기공 크기의 가스 분리 탄화 규소 멤브레인을 제조하기 위해 저비용 폴리머 전구체를 찾을 수 있습니다. 또한 소결 첨가제의 조합을 최적화하고 소결 온도를 낮추며 공동 소결 기술의 적용 범위를 더욱 확장할 수 있습니다.
환경 보호에 대한 세계적인 관심으로 인해 고성능 여과 및 분리 기술에 대한 수요가 점점 더 시급해지고 있으며 이는 탄화 규소 멤브레인 튜브의 개발 및 적용에 귀중한 기회를 제공합니다. 앞으로도 미성숙 세라믹 분리막 생산 및 제조 기술의 문제를 해결하기 위해서는 여전히 많은 자원이 필요하므로 탄화규소 세라믹 분리막 기술이 보다 실용적으로 활용될 수 있습니다.